DURUS is the result of a DARPA-sponsored project to improve the efficiency of humanoid robots. The work was carried out at SRI international. For this project we looked at every aspect of a humanoid system and identified the main areas in which energy loss could be improved. We chose to focus on the walking gait, the drive electronics and the mechanical transmissions.
The walking gait, developed by Amber Labs, employs Hybrid Zero Dynamics, rather than the standard ZMP walking algorithm. The result is a very natural-looking, upright, dynamic and energy-efficient walking gait.
High efficiency electronics deliver up to 200A to low-cost hobby motors, which are more difficult to control than state-of-the-art BLDCs but if handled properly can deliver comparable performance at less than 1/10th the cost.
DURUS uses custom drive transmissions which eliminate sliding friction, resulting in a drivechain that is 97% efficient. DURUS does not use series elastic actuators, but instead incorporates passive springs in the ankles, allowing it efficiently to absorb the energy of impacts with the ground and reuse it on the next stride.
DURUS won the Endurance Challenge at the DARPA Robotics Challenge in June 2015, demonstrating dynamic 3D walking for over 3 hours on a single 1.1KWh battery. The robot demonstrated a cost of transport of 1.5, making it one of the most efficient fully-actuated humanoids in the world.
DURUS was my baby. I was the lead mechanical designer and oversaw the integration of the whole system. Work on the novel transmissions had already started when I joined SRI, but I took over control of the design and optimized the transmission design for maximum efficiency. I designed the entire lower body, including the actuators, and employed and supervised a contractor to design the battery packs and torso structure.
Notable features of my design include:
Novel transmissions with 97% efficiency
Stiff and lightweight design. The whole system weighs under 100Kg.
Low inertia leg design, with the heaviest components positioned near the top of the leg. This minimizes energy consumption during swing phase.
Custom, low-cost torque sensors
Very high resolution (21-bit) absolute sensors, enabling higher control gains for increased responsiveness.
2-DOF ankle with a large range of motion, which incorporates linear springs to store and release energy during dynamic walking
This work was done while I was employed at SRI International.
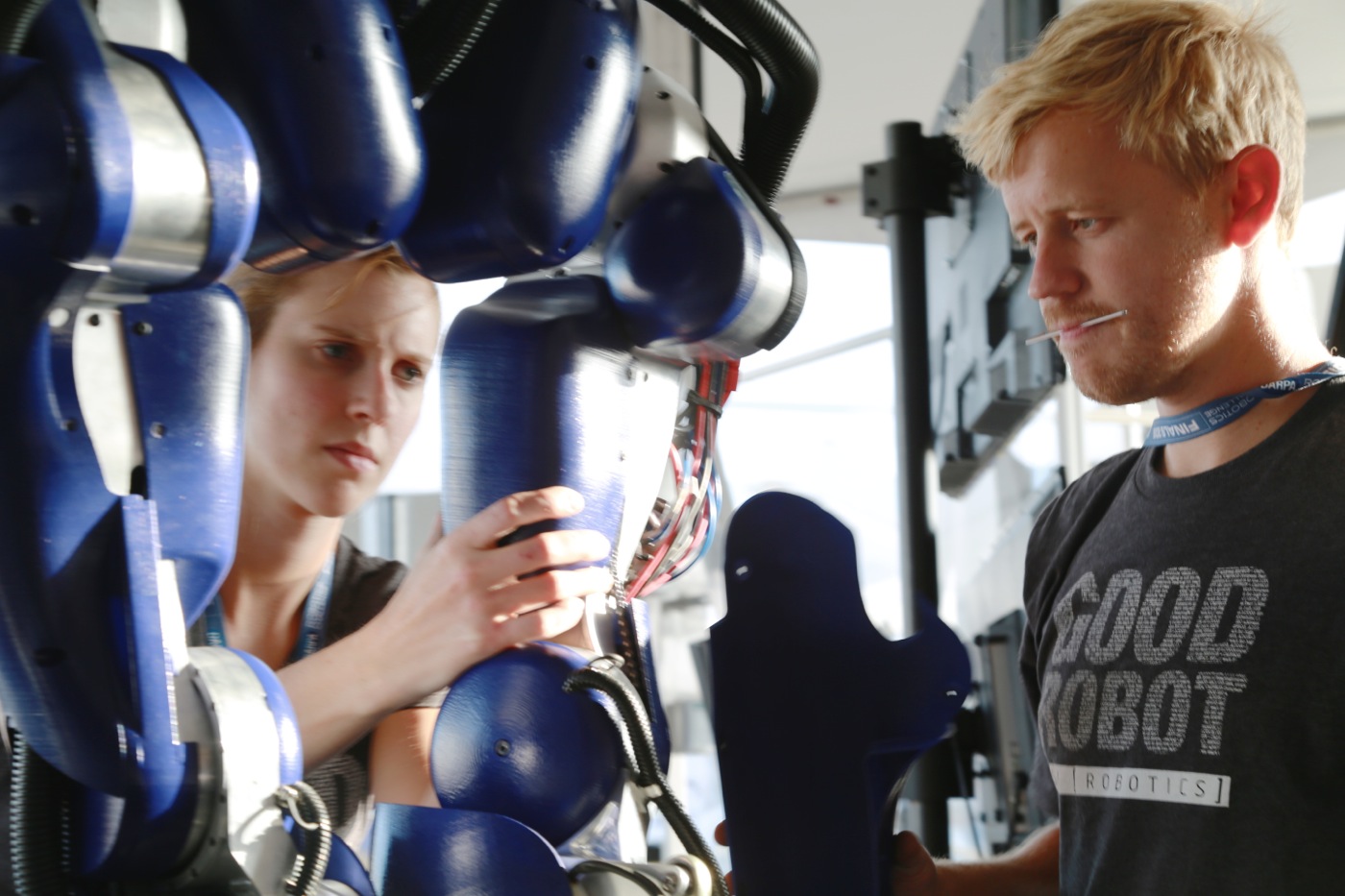
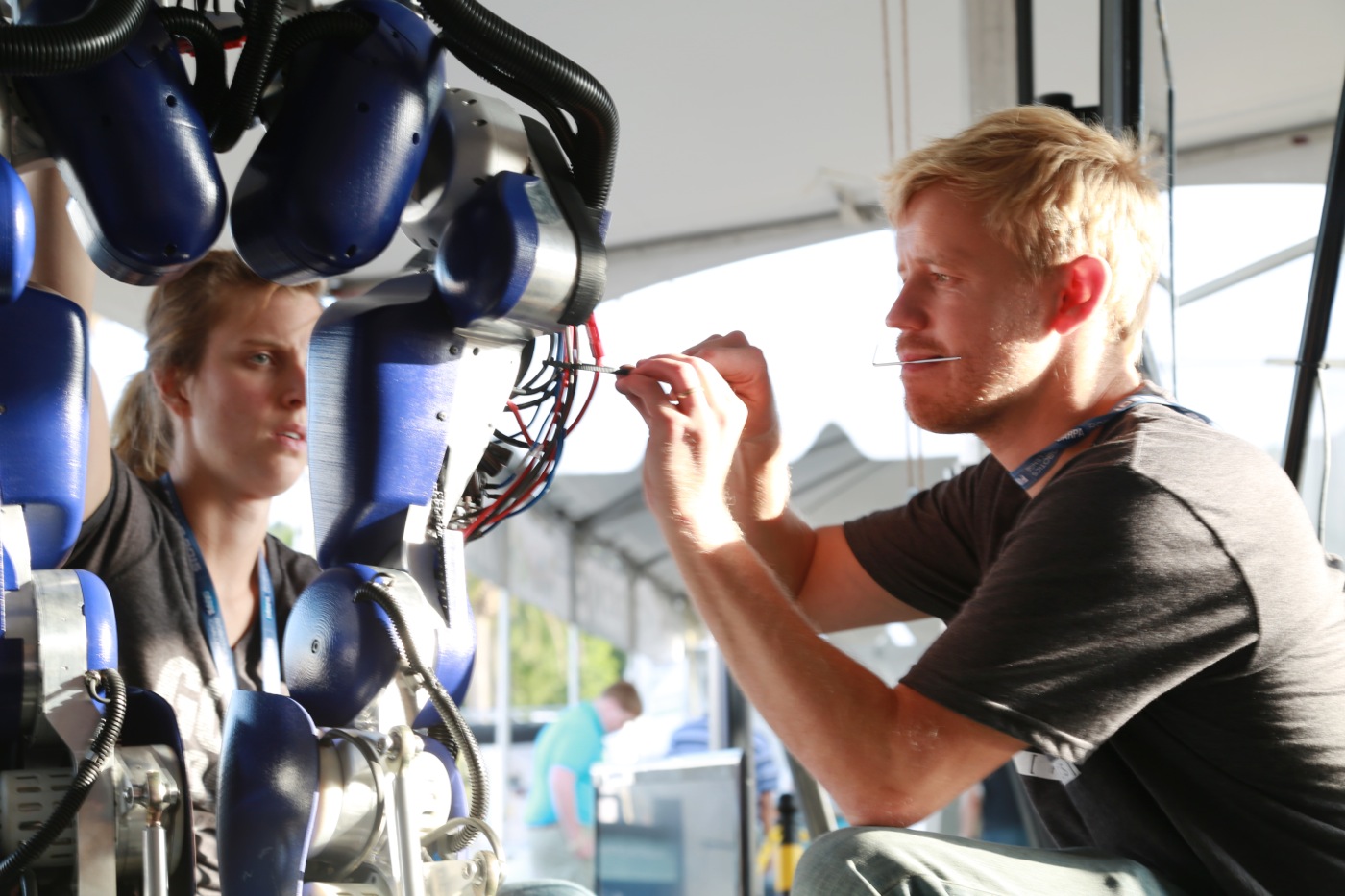
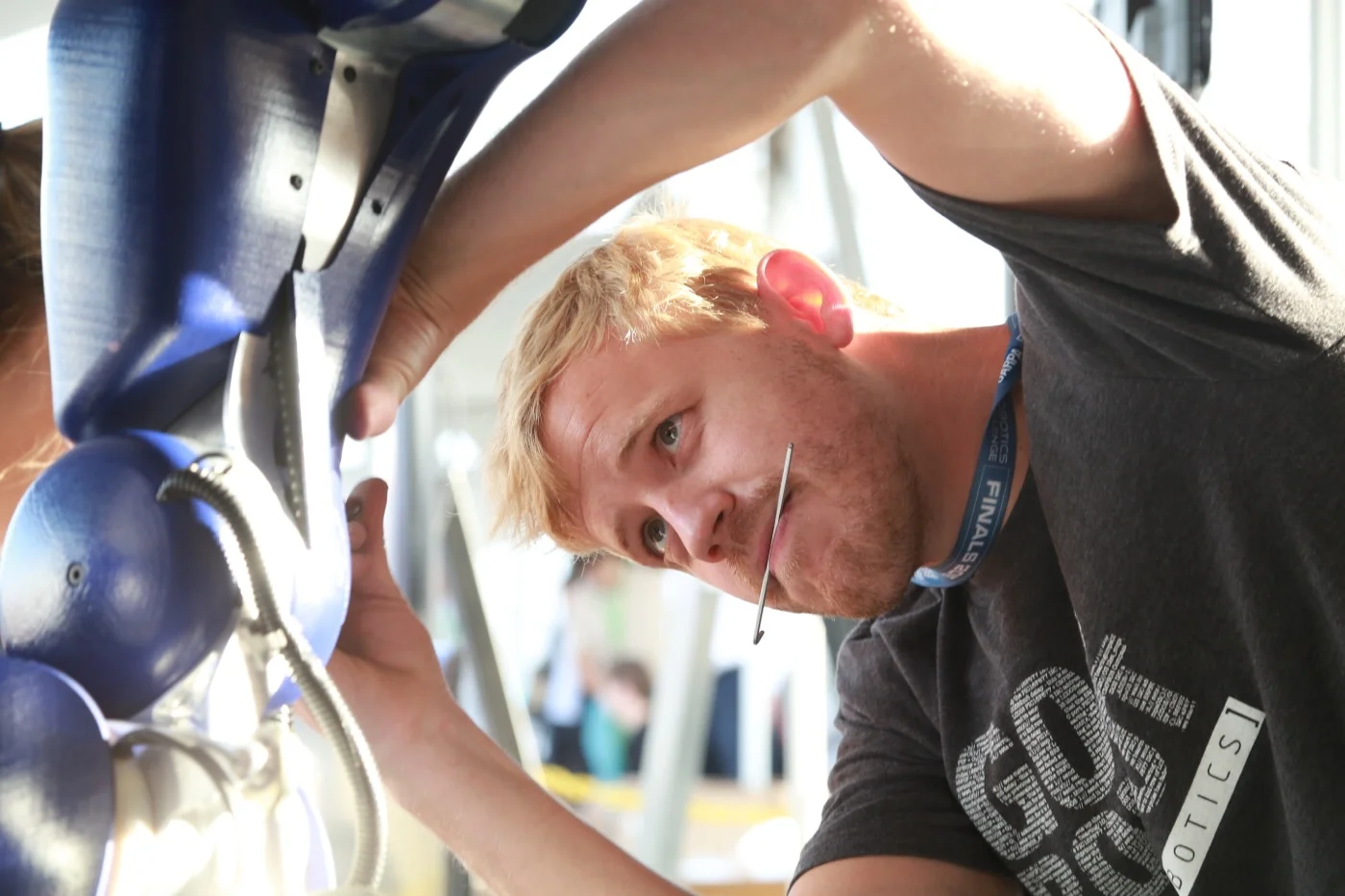
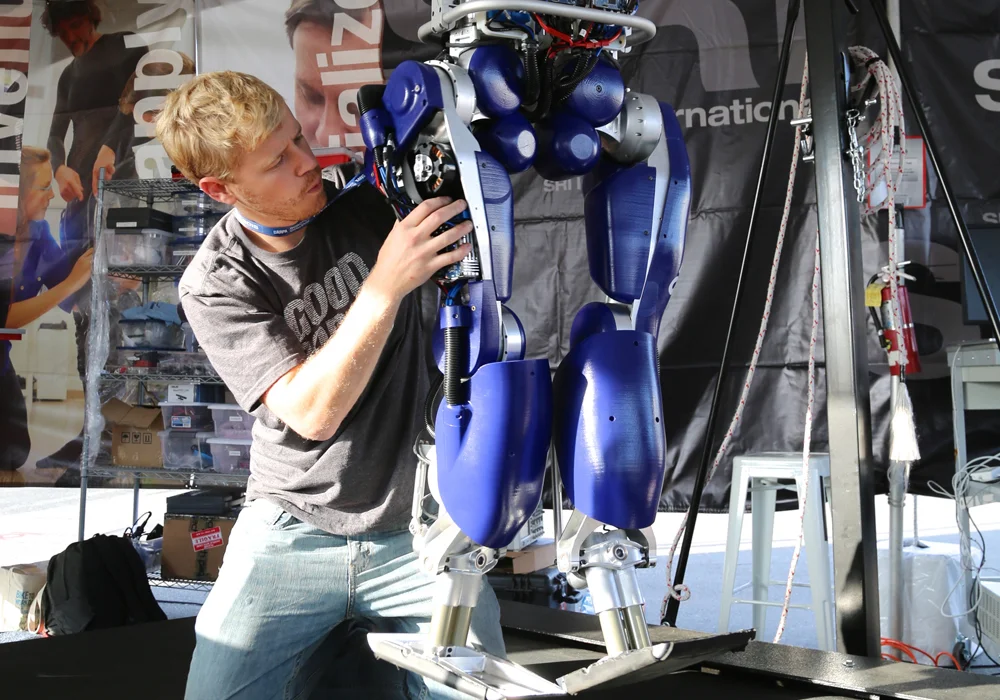
Images and videos courtesy of SRI International.